Продолжая использовать сайт, вы даете свое согласие на работу с этими файлами.
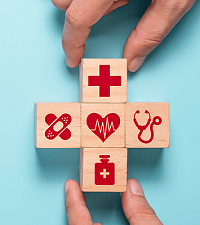
Electrodeionization
Electrodeionization (EDI) is a water treatment technology that uses DC power, ion exchange membranes, and ion exchange resin to deionize water. EDI is usually a polishing treatment to reverse osmosis (RO). EDI differs from other RO polishing technologies such as chemically regenerated mixed beds, in that it is continuous and requires no chemical regeneration. EDI is sometimes referred to as continuous electrodeionization (CEDI) since the electric current regenerates the ion exchange resin mass continuously. The CEDI technique can achieve high purity, with product conductivity on the order of 0.1 μS/cm and sometimes with resistivity as high as 18.2 MΩ-cm. Electrodeionization (EDI) is a combination of three different processes: Electrolysis, where with a continuously applied electric DC current, both positive and negative ions are directed to the electrode that has opposing electrical charge; the electrical potential pulls anions and cations from diluting chambers, though cation or anion exchange membranes, into concentrating chambers. Ion exchange, where ion exchange resin makes up the diluting chambers, and the cations and anions are affixed to resin sites as water passes through the resin bed; and chemical regeneration, which occurs by water splitting. In a chemically regenerated mixed bed, the hydrogen (H+) of acid regenerates cation resin. The hydroxide (OH-) of sodium hydroxide (caustic soda) regenerates anion resin. In EDI, the electrical current causes water to split from H2O → H+ + OH-, regenerating the resin without the need for addition of external chemicals.
Quality of the feed
To maximize purity of the product, EDI feed water needs pre-treatment, usually reverse osmosis. Feed water must follow certain requirements to prevent damage to the instrument.
Common parameters are:
- Hardness of feed water < 1 ppm as CaCO3, with limited exceptions up to 2 ppm.
- Silica content (SiO2) must be < 1ppm in most EDI cells or < 2 ppm in thin cell modules.
- CO2 must be monitored to prevent excessive loading of anion exchange resin.
- TOC, which can foul resins and membranes, must be minimized.
- Chlorine, ozone and other oxidizers can oxidize resins and membranes and create permanent damage, and must be minimized.
History
To eliminate or minimize the concentration polarization phenomenon present in electrolysis systems of the time, electrodeionization was developed in the early 1950s. A patent on the technology was filed in 1953, and subsequent publications popularized the technology.
The technology was limited in application because of the low tolerance of total dissolved solids, hardness and organics. During the 1970s and 1980s, reverse osmosis became a preferred technology to ion exchange resin for high TDS waters. As RO gained popularity, it was determined that EDI would be a suitable polishing technology. Packaged RO and EDI systems were used to displace chemically regenerated ion exchange systems.
In 1986 and 1989, several companies including Millipore, Ionpure, HOH Water Technologies, and Ionics Inc. developed electrodeionization devices. The initial devices were large, costly, and often unreliable. However, in the 1990s, smaller and less costly modular designs were introduced, some of which minimized leakage. Nonetheless, these designs and their contemporary descendants still face limitations such as cost and limited operational envelope.
Applications
When fed with low total dissolved solids feedwater (e.g. purified by RO), the product can reach very high purity levels, with conductivity on the order of 0.5 μS/cm. The ion exchange resins act to keep the ions, allowing these to be transported across the ion exchange membranes. The main applications of EDI technology, are in electronics, pharmaceuticals, and power generation. In electronics, deionized water is used to rinse components during manufacturing. The electronic chips are very small, with little free space between component elements. Therefore, very low numbers of ions are necessary to conduct undesired electricity between components. If this occurs, a short circuit may result and make the chip unusable. In the pharmaceutical industry, the presence of ions in water used in drug development can lead to undesired side reactions and introduce harmful impurities. In power generation, the presence of ions in boiler feed water can lead to buildup of solids or degradation of boiler walls, both of which can lower boiler efficiency and present safety hazards. Due to the large financial and safety concerns present in these industries, they provide the bulk of the revenue for EDI developers. Electrodeionization systems have also been applied for the removal of heavy metals from different types of wastewater such as mining, electroplating, and nuclear processes. The primary ions removed in these processes are chromium, copper, cobalt, and cesium, though EDI sees use in the removal of others as well.
Theory
Electrodes in an electrochemical cell are referred to as either anodes or cathodes. The anode is defined as the electrode at which electrons leave the cell and oxidation occurs, and the cathode is the electrode at which electrons enter the cell and reduction occurs. Each electrode may become either the anode or the cathode, depending on the voltage applied to the cell.
Each deionization cell consists of an electrode and an electrolyte with ions that undergo either oxidation or reduction. An electrolyte is a substance containing free ions that behave as an electrically conductive medium. Because they commonly consist of ions in solution, the electrolytes are often known as ionic solutions, but molten and solid electrolytes are also possible.
Water is passed between an anode (positive electrode) and a cathode (negative electrode). Ion-selective membranes allow the positive ions to separate from the water toward the negative electrode and the negative ions toward the positive electrode. As a result, the ions cannot escape the cell, and deionized water is produced.
In situ regeneration
When using current that is higher than the necessary for the movement of the ions, a portion of the incident water will be split, forming OH- and H+. This species will replace the impurity anions and cations in the resin. This process is called in situ regeneration of the resin. As it occurs during the deionization process, it has the benefit of allowing for continuous purification, as opposed to requiring a pause in operation to manually chemically regenerate ion exchange resin in other deionization techniques.
Installation scheme
The typical EDI installation has the following components: electrodes, anion exchange membrane, cation exchange membrane, and resin. The most simplified configuration comprises three compartments. To increase production, the number of compartments or cells can be increased as desired.
Once the system is installed and feedwater begins to flow through the system, cations flow toward the cathode and the anions flow toward the anode. Only anions can go through the anion exchange membrane and only cations can go through the cation exchange membrane. This configuration allows anions and cations to only flow in one direction because of the selectivity of the membranes and the electric force, leaving the feed water free of ions. It also allows for the separate collection of cation and anion concentration flows, creating the opportunity for more selective waste disposal; this is especially useful in the removal of heavy metal cations.
The concentration flows (right and left of the feed flow) are rejected and they can be wasted, recycled, or used in another process.
The purpose of the ion exchange resin is to maintain stable conductance of the feed water. Without the resin, ions can be removed initially, but the conductance will drop dramatically as the concentration of ions decreases. With lower conductance, the electrodes are less able to direct the flow of electrons and remove them; with the addition of resins, a steady rate of removal is possible, and the remaining ion concentration in the processed water is lower by orders of magnitude.
See also
External links
- video.
- Continuous Electrodeionization (CEDI/EDI) Ionpure CEDI Products
- Bộ lọc nước phèn
- Electrodeionization Technology
- EDI History
- Electrodeionization Systems, Electrodeionization Systems
- Advanced Electrodeionization Technology for Product Desalting, Argonne National Laboratory